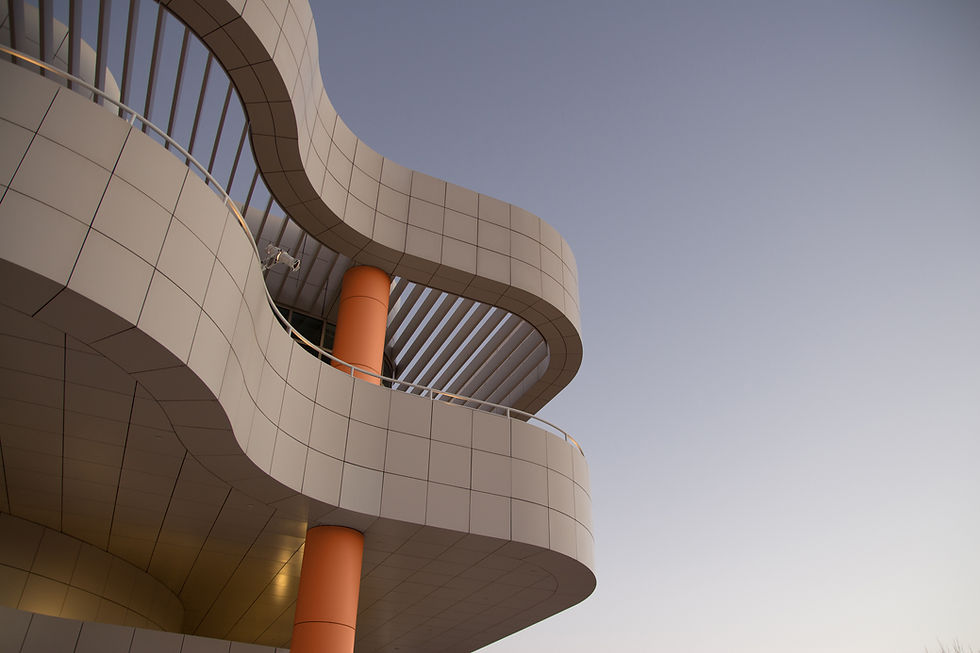
In the realm of interior design and architectural materials, printed quartz slabs are rapidly gaining acclaim for their durability, beauty, and customization options. However, an exciting advancement within this category is the emergence of full-body printing technology. This innovation extends beyond the surface, offering a more realistic, consistent, and durable material for high-end interiors.
In this blog, we’ll delve into full-body printing technology for quartz slabs, explore how it differs from traditional surface printing, and discuss why it’s becoming a game-changing solution for architects, designers, and homeowners.

What is Full Body Printing Technology?
Full-body printing technology in quartz slabs involves embedding designs and patterns throughout the entire thickness of the slab, rather than just on the surface. Unlike traditional surface printing, which only decorates the outermost layer, full-body printing ensures that the pattern is consistent from top to bottom.
This technique replicates the natural appearance of stones like marble or granite, where veining and patterns run through the entire material. Full-body printed quartz offers the same visual depth and natural look as stone, combined with the enhanced durability and benefits of modern quartz engineering.
How Does Full Body Printing Work in Quartz Slabs?
Full-body printing combines advanced digital printing technology with engineered quartz. Here’s an overview of the process:
Composition: Similar to traditional quartz, full-body printed quartz slabs consist of 90-95% natural quartz crystals mixed with resins and pigments, creating a robust and durable material.
Layering the Pattern: During manufacturing, the pattern or veining is embedded throughout the entire thickness of the slab, not just on the surface. This is achieved through multi-layer printing technology, ensuring consistent patterns are visible at every point in the material.
Curing Process: After printing, the slab undergoes a curing process, which solidifies the printed design into the quartz composite, making the pattern an integral part of the slab’s structure.
Final Finishing: The slab is then polished, honed, or given other finishes based on the desired design.